Slip rings are essential components in many industries, allowing the transmission of power and data between stationary and rotating parts of a machine. These devices are crucial for the functionality of various equipment, from wind turbines to medical imaging systems. However, standard slip rings may not always meet the unique demands of every application. This is where custom slip rings come into play. Custom slip rings are designed to address specific requirements, offering tailored solutions that ensure optimal performance and reliability. By accommodating unique specifications such as size, electrical capacity, and environmental resistance, custom slip rings provide a level of precision and efficiency that standard models cannot achieve. Their adaptability makes them indispensable in specialized industrial applications.
Understanding Custom Slip Rings
Definition and Purpose of Custom Slip Rings
Custom slip rings are specialized electromechanical devices designed to meet the specific needs of various industrial applications. Unlike standard slip rings, which come in predefined configurations and sizes, custom slip rings are tailored to fit the unique requirements of a particular system or machinery. They facilitate the transmission of power, electrical signals, or data between stationary and rotating parts of equipment, ensuring continuous and reliable operation.
The primary purpose of custom slip rings is to provide a solution that is precisely aligned with the operational demands of a specific application. This includes considerations such as the number of circuits, voltage and current ratings, rotational speed, environmental conditions, and physical dimensions. By addressing these unique needs, custom slip rings enhance the performance, efficiency, and longevity of the equipment they are integrated into.
Common Industries and Applications that Benefit from Custom Solutions
Custom slip rings are integral to a wide range of industries, each with distinct operational challenges and requirements. Some of the key sectors that benefit from these tailored solutions include:
1. Aerospace and Defense
In the aerospace and defense industry, equipment such as radar systems, satellite communication devices, and missile guidance systems often operate under extreme conditions. Custom slip rings designed for this sector must withstand high temperatures, vibrations, and shocks. They ensure the seamless transmission of critical data and power in applications where failure is not an option.
2. Medical Equipment
Medical imaging devices, such as MRI and CT scanners, rely heavily on custom slip rings. These machines require precise and uninterrupted data transmission to produce accurate diagnostic images. Custom slip rings in this industry are designed to meet stringent cleanliness standards and to operate reliably in sterile environments.
3. Renewable Energy
Wind turbines are a prime example of renewable energy applications that utilize custom slip rings. These devices enable the transfer of electrical power from the rotating blades to the stationary power grid. Custom slip rings are engineered to handle high power loads, resist harsh weather conditions, and ensure minimal maintenance over the turbine’s lifespan.
4. Industrial Automation
In the field of industrial automation, custom slip rings are used in robotic arms, assembly lines, and packaging machinery. These applications require high-speed data and power transmission with minimal interference. Custom slip rings are designed to fit within compact spaces and to deliver consistent performance despite continuous rotation and varying operational demands.
5. Maritime and Offshore
Marine applications, such as underwater remotely operated vehicles (ROVs) and offshore drilling rigs, also benefit from custom slip rings. These environments demand robust solutions that can resist corrosion, water ingress, and pressure changes. Custom slip rings for maritime use are tailored to provide reliable connectivity in the challenging conditions of the sea.
6. Telecommunications
Custom slip rings are vital in the telecommunications sector, particularly in antenna systems and communication satellites. These applications require the precise transmission of high-frequency signals. Custom slip rings are designed to maintain signal integrity and to support the high-speed rotation of antennas, ensuring uninterrupted communication.
In addition to these industries, custom slip rings find applications in various other fields such as agriculture, automotive, and entertainment. Each application presents unique challenges that standard slip rings may not be able to address effectively. Custom solutions offer the flexibility to design slip rings that meet specific operational requirements, leading to improved performance and reduced downtime.
Advantages of Custom Slip Rings
One of the significant advantages of custom slip rings, including capsule slip rings, is their ability to enhance the overall efficiency and reliability of the equipment they are integrated into. By providing a tailored solution, custom slip rings ensure that the specific electrical and mechanical needs of an application are met. This leads to optimal performance and can significantly extend the lifespan of the equipment.
Another key benefit is the reduction in maintenance requirements. Custom slip rings, are designed to withstand the specific environmental and operational conditions they will encounter, leading to fewer breakdowns and less frequent servicing. This not only reduces maintenance costs but also minimizes downtime, which is critical in industries where continuous operation is essential.
Custom slip rings also offer improved signal integrity and power transmission capabilities. By optimizing the design to meet the exact specifications of the application, custom slip rings can reduce electrical noise, improve data accuracy, and ensure consistent power delivery. This is particularly important in applications where precision and reliability are paramount.
The use of custom slip rings, can lead to overall cost savings. While the initial investment may be higher compared to standard slip rings, the long-term benefits of reduced maintenance, improved performance, and extended equipment life can result in significant cost efficiencies over time.
Custom slip rings provide a vital solution for a wide range of industries with specific operational needs. Their ability to offer tailored performance, reliability, and efficiency makes them indispensable in many high-demand applications. Whether it’s in aerospace, medical equipment, renewable energy, industrial automation, maritime operations, or telecommunications, custom slip rings play a crucial role in ensuring the smooth and uninterrupted operation of complex machinery and systems. The flexibility and precision they offer make them a preferred choice over standard slip rings, particularly in environments where standard solutions fall short.
Designing Custom Slip Rings
Designing custom slip rings requires careful consideration of various factors to ensure they meet the specific needs of the application. This section delves into the critical aspects involved in designing custom slip rings, highlighting the role of application engineers in developing these tailored solutions.
Key Considerations in Designing Custom Slip Rings
Mechanical Requirements
The mechanical requirements of custom slip rings are fundamental to their design. These requirements include the dimensions, rotational speed, and physical configuration of the slip ring. The dimensions must be tailored to fit the specific spatial constraints of the machinery. This involves specifying the outer diameter, length, and center bore diameter, which must align perfectly with the existing components of the equipment.
Rotational speed, measured in RPM (revolutions per minute), is another crucial factor. The slip ring must be designed to operate efficiently at the required speed without causing excessive wear or generating undue heat. The materials used for the slip ring must also be chosen based on their ability to withstand the operational stresses and environmental conditions, ensuring longevity and reliability.
Electrical Connections
Electrical connections in custom slip rings are designed to meet the specific power and signal transmission needs of the application. This involves determining the number of circuits, voltage and current ratings, and the type of signals to be transmitted. For instance, in applications that require the transmission of high-definition data, such as Ethernet slip rings, the design must accommodate high-speed data channels while ensuring minimal signal loss and interference.
The type of connectors used on both the rotating and stationary parts of the slip ring is also essential. These connectors must be robust and reliable, capable of maintaining consistent contact throughout the operation. Options include wires with no connectors, connectors on cables, or connectors integrated into the slip ring body. The choice depends on the specific requirements of the application and the environmental conditions it will face.
Environmental Factors
Environmental factors play a significant role in the design of custom slip rings. These factors include temperature, humidity, exposure to dust and water, and potential exposure to corrosive substances. The slip ring must be designed to operate reliably under these conditions, which may involve selecting materials that are resistant to corrosion and wear.
The enclosure IP rating is an important consideration, indicating the level of protection against dust and water ingress. For applications in harsh environments, a higher IP rating may be required to ensure the slip ring remains operational despite adverse conditions. Additionally, the operating temperature range must be specified to ensure the materials and components can withstand the expected temperature variations without degrading in performance.
The Role of Application Engineers in Developing Tailored Solutions
Application engineers play a crucial role in the design and development of custom slip rings. Their expertise and experience are vital in translating the specific requirements of an application into a functional design. Here’s how they contribute to the process:
Requirements Analysis
Application engineers begin by conducting a thorough analysis of the application’s requirements. This involves understanding the operational needs, environmental conditions, and mechanical and electrical specifications. By working closely with the client, they gather detailed information that forms the basis for the custom slip ring design.
Design and Prototyping
Using the gathered information, application engineers create a detailed design that addresses all the key considerations. This design process often involves the use of advanced software tools to model the slip ring and simulate its performance under various conditions. Once the design is finalized, a prototype is developed and tested to ensure it meets the required specifications.
Testing and Validation
The prototype undergoes rigorous testing to validate its performance. This includes testing for mechanical durability, electrical performance, and environmental resilience. Application engineers analyze the test results and make necessary adjustments to the design to ensure optimal performance. This iterative process continues until the custom slip ring meets all the required criteria.
Implementation and Support
Once the design is validated, the custom slip ring is manufactured and implemented into the application. Application engineers provide ongoing support during the installation and operational phases to ensure smooth integration and address any issues that may arise. Their role is critical in ensuring the custom slip ring performs as intended and delivers the expected benefits.
Designing custom slip rings is a complex process that involves careful consideration of mechanical, electrical, and environmental factors. The expertise of application engineers is essential in developing tailored solutions that meet the specific needs of an application. By addressing these key considerations and leveraging their specialized knowledge, application engineers ensure that custom slip rings provide reliable, efficient, and long-lasting performance in various industrial applications. Whether it’s for transmitting high-speed data through ethernet slip rings or ensuring robust power delivery in harsh environments, custom slip rings are designed to meet the unique challenges of each application.
Mechanical and Electrical Specifications
When designing custom slip rings, understanding and specifying the mechanical and electrical requirements are crucial to ensuring optimal performance and longevity. This section provides a detailed discussion on these critical specifications.
Mechanical Specifications
RPM (Revolutions Per Minute)
The RPM rating of a custom slip ring is a fundamental mechanical specification. It indicates the maximum speed at which the slip ring can operate effectively without compromising performance or durability. High RPM ratings are essential for applications involving rapid rotation, such as those found in industrial automation and medical imaging equipment. The slip ring must be designed to handle these speeds while minimizing wear and maintaining reliable contact between rotating and stationary components.
Enclosure IP Rating
The Ingress Protection (IP) rating is another crucial mechanical specification that defines the level of protection the slip ring offers against dust and water. The IP rating is composed of two digits: the first indicates protection against solid particles, and the second indicates protection against liquids. For instance, an IP65 rating means the slip ring is dust-tight and protected against low-pressure water jets from any direction. This rating is particularly important for slip rings used in harsh environments, such as offshore wind turbines or outdoor surveillance systems, where exposure to dust, water, and other contaminants is common.
Operating Temperature
The operating temperature range specifies the minimum and maximum temperatures within which the slip ring can function effectively. This specification ensures that the materials and components used in the slip ring can withstand temperature extremes without degrading in performance. For example, slip rings used in aerospace applications must operate reliably in both high-altitude, low-temperature conditions and high-temperature environments near engines or other heat sources. Designing for a broad operating temperature range ensures the slip ring can perform consistently under varying environmental conditions.
Dimensions
The physical dimensions of a custom slip ring, including its outer diameter, length, and center bore diameter, are tailored to fit the specific spatial constraints of the application. These dimensions are critical for ensuring the slip ring integrates seamlessly with the existing machinery or system. In compact or space-limited applications, such as in robotics or medical devices, the slip ring must be designed to occupy minimal space while still providing all necessary functions. Precise dimensioning ensures that the slip ring can be installed without requiring significant modifications to the surrounding equipment.
Electrical Connection Options
Wire Types and Connectors
The choice of electrical connections in a custom slip ring significantly impacts its performance and reliability. Custom slip rings can be designed with various wire types and connectors to suit different application needs. Options include:
Wires with No Connectors: This option is suitable for applications where the slip ring will be directly soldered or integrated into a larger assembly. It provides flexibility in connecting to other components but requires careful handling during installation.
Connectors on Cables: Pre-installed connectors on cables simplify the installation process and ensure a secure, reliable connection. This option is ideal for applications where ease of installation and maintenance is a priority.
Connectors on the Slip Ring Body: Integrating connectors directly onto the slip ring body can provide a more compact and robust solution. This design minimizes the risk of loose connections and is beneficial in environments with high vibrations or movement.
Channel Count and Signal Types
The number of channels and the types of signals the slip ring can transmit are vital electrical specifications. Custom slip rings can be designed to handle various signals, including power, data, and control signals. For example, ethernet slip rings are specifically designed to transmit high-speed data signals without interference, making them essential in applications requiring reliable data communication, such as in telecommunications and data acquisition systems.
Voltage and Current Ratings
The voltage and current ratings of a custom slip ring determine its capacity to transmit electrical power safely and efficiently. These ratings must be specified based on the application’s requirements to prevent overheating and ensure long-term reliability. High-power applications, such as those in industrial machinery or renewable energy systems, require slip rings with high voltage and current ratings to handle significant power loads without compromising performance.
Shielding and Noise Reduction
For applications involving sensitive data transmission, such as those using ethernet slip rings, proper shielding and noise reduction are critical. Custom slip rings can be designed with shielding to protect against electromagnetic interference (EMI) and ensure signal integrity. This is particularly important in environments with high electrical noise, where maintaining clear and accurate signal transmission is essential.
Understanding and specifying the mechanical and electrical requirements of custom slip rings is essential for designing solutions that meet the unique demands of various applications. By carefully considering factors such as RPM, IP rating, operating temperature, dimensions, and electrical connection options, designers can create custom slip rings that provide reliable and efficient performance. Whether for transmitting high-speed data in ethernet slip rings or ensuring robust power delivery in industrial settings, these specifications are critical to the success of the application.
Advantages of Custom Slip Rings
Custom slip rings offer numerous advantages over standard, off-the-shelf solutions. These benefits stem from their tailored design, which addresses the specific needs and challenges of various applications. In this section, we will explore the enhanced performance and reliability, the tailored solutions for unique application needs, and the long-term cost benefits and efficiency improvements that custom slip rings provide.
Enhanced Performance and Reliability
One of the primary advantages of custom slip rings is their enhanced performance and reliability. Because they are designed to meet specific application requirements, custom slip rings can be optimized for the exact operational conditions they will face. This optimization leads to several performance benefits:
1. Improved Electrical Contact:
Custom slip rings can be designed with superior materials and contact technologies that reduce electrical resistance and wear. This ensures consistent and reliable transmission of power and signals, even in demanding conditions. For instance, gold-gold contacts are often used in high-performance slip rings to provide low resistance and long-lasting durability.
2. Optimal Signal Integrity:
In applications where signal integrity is critical, such as in telecommunications or data transmission systems, custom slip rings can be engineered to minimize electrical noise and interference. This ensures that data signals are transmitted accurately and without loss, which is crucial for maintaining the performance of the entire system.
3. Robustness in Harsh Environments:
Custom slip rings can be built to withstand extreme environmental conditions, such as high temperatures, dust, moisture, and corrosive substances. This robustness is achieved through careful selection of materials and protective enclosures, such as high IP ratings that safeguard against ingress of dust and water.
Tailored Solutions for Unique Application Needs
Another significant advantage of custom slip rings is their ability to provide tailored solutions for unique application needs. This customization ensures that the slip ring fits perfectly within the specific operational and spatial constraints of the application:
1. Precise Fit and Integration:
Custom slip rings are designed to match the exact dimensions required by the equipment, including outer diameter, length, and center bore diameter. This precise fit allows for seamless integration into existing systems without the need for extensive modifications.
2. Specific Electrical Specifications:
The electrical specifications of custom slip rings, such as the number of circuits, voltage and current ratings, and types of signals, can be customized to meet the specific needs of the application. Whether it’s for high-power transmission in industrial machinery or high-speed data transfer in telecommunications, custom slip rings can be configured to handle the exact electrical requirements.
3. Application-Specific Features:
Custom slip rings can incorporate features that address unique operational challenges. For example, in applications requiring continuous rotation at high speeds, custom slip rings can be designed with advanced bearing systems to reduce friction and wear. Similarly, for applications exposed to electromagnetic interference, custom slip rings can include shielding to protect signal integrity.
Long-Term Cost Benefits and Efficiency Improvements
While custom slip rings may have a higher initial cost compared to standard solutions, they offer significant long-term cost benefits and efficiency improvements:
1. Reduced Maintenance Costs:
Custom slip rings are designed for durability and reliability, which translates to fewer breakdowns and lower maintenance requirements. The use of high-quality materials and optimized designs reduces wear and tear, leading to longer operational lifespans and less frequent need for repairs or replacements.
2. Minimized Downtime:
The reliability of custom slip rings means that systems experience less downtime due to slip ring failures. This is particularly important in critical applications where downtime can lead to significant productivity losses or safety risks. By ensuring continuous and reliable operation, custom slip rings help maintain overall system efficiency.
3. Enhanced Operational Efficiency:
Custom slip rings can improve the overall efficiency of the equipment by providing better electrical performance, reducing energy losses, and ensuring optimal signal transmission. This efficiency translates to better performance of the entire system, which can lead to increased productivity and lower operational costs over time.
4. Long-Term Cost Savings:
Although the upfront investment in custom slip rings may be higher, the long-term savings from reduced maintenance, minimized downtime, and improved operational efficiency can outweigh the initial costs. Custom slip rings are a cost-effective solution in the long run, providing value through their extended service life and reliable performance.
Custom slip rings offer a range of advantages that make them an attractive choice for many applications. Their enhanced performance and reliability, tailored solutions for unique needs, and long-term cost benefits and efficiency improvements highlight the value they bring to various industries. By investing in custom slip rings, businesses can ensure their equipment operates at peak efficiency, with reduced maintenance costs and improved overall performance.
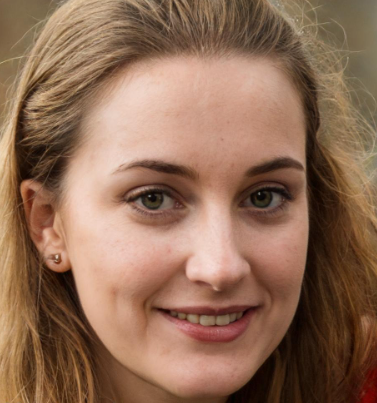
Brandy Stewart, an enchanting wordsmith and seasoned blogger, weaves compelling narratives that transport readers to uncharted territories. Infused with perceptive viewpoints and dynamic storytelling, Doris exhibits a command of language that enthralls both hearts and minds, leaving a lasting mark on the literary panorama.